Hydrogen storage in porous metal hydride polymer hybrid materials
VIDEO
coming soon...
Introduction
Hydrogen is an irreplaceable energy vector of a carbon-neutral future, but high-performance storage must be available to allow its widespread usage. Promising candidates for solid-state hydrogen storage are metal hydrides, with examples of such hydride-forming metals being FeTi [1], Mg, LaNi5, and high-entropy alloys. Metal hydrides provide high volumetric energy densities, safety, and efficiency, holding the promise to be the superior storage option. However, many hurdles, including sluggish (initial) kinetics and insufficient (mechanical and chemical) stability, still need to be surmounted.
Within the SCoRe A+ initiative, this project aims to tackle the mentioned problems by prototyping nanoporous metal hydride-polymer composites, as illustrated in Figure 1. The project encompasses all required steps for achieving this - from synthesis over structural characterization to functional optimization. Nanoporous materials can exhibit excellent properties, such as high surface-to-volume ratio, high strength-to-weight ratio, and electrical and thermal conductivity [2]. The large surface area is especially essential for rapid hydrogen absorption. Furthermore, the pores are infiltrated with a polymer that provides mechanical stability and selective hydrogen gas permeability [3]. Additionally, the polymer adds another degree of freedom for engineering a high-performance storage material with minimal detrimental effects on the gravimetric storage density. The investigated material systems include FeTi [1], a chemically simple and well-studied model system, and promising high-entropy alloys, e.g., TiZrVNbHf [4].
Method
To create an FeTi-based nanocomposite, the FeTi powder is blended with an immiscible sacrificial phase using high-pressure torsion and consolidated into a bulk sample. The severe plastic deformation leads to a mixture of storage and sacrificial phases at the micro- or nanoscale, resulting in simultaneous grain refinement and an increased defect density. The latter can significantly improve the hydrogen sorption properties.
In the next step, the sacrificial phase is dissolved by a selective wet chemical process. This results in a nanoporous FeTi foam. Depending on the structure, i.e., the FeTi and Cu grain sizes of the initial nanocomposites, different pore and ligament sizes can be achieved, allowing to tune the metallic foam structure.The remaining porous FeTi can be additionally stabilized with a suitable polymer binder. Such binder can serve as a pure mechanical stabilization, e.g., epoxy resins, or have additional functional properties, e.g., PMMA. The processes involved in preparing the hybrid material are schematically illustrated in Figure 1.
The investigations involve detailed structural characterization of the composition, nano- and microstructure, as well as morphology. In particular, the aim is to understand the impact and interplay of various interfaces (surfaces, grain boundaries, phase boundaries) on the material's (hydrogen sorption) properties. Primary characterization methods include electron microscopy (SEM, TEM) and (Synchrotron) X-ray diffraction. We complementarily probe the mechanical properties using micro- and nanoindentation. Such experiments performed on pristine and cycled materials provide detailed insights regarding potential changes and aging effects due to hydrogen absorption and desorption.
The hydrogen sorption performance is investigated using a Sievert's apparatus, loading the materials using gaseous hydrogen and enabling the determination of capacity, kinetics, and long-term cyclability. Additionally, electrochemical loading is performed to supplement the data obtained by the gas sorption experiments. Altogether, this provides extensive knowledge of the chemistry, phase composition, morphology, and nanostructure and their interactions with the storage properties of the material system.
Properties and Performance
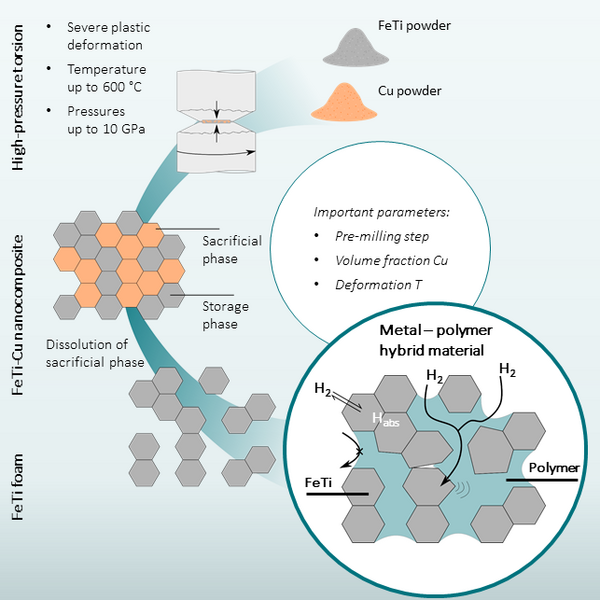
Results and discussion
A first milestone was achieved by preparing a homogeneous FeTi-Cu nanocomposite with tunable grain size and distinct mechanical alloying. The intermetallic compound FeTi has high strength and is brittle, while Cu exhibits low strength and good deformability. Although the latter adds the necessary deformability to the composite, efficient refinement of the respective phases to the nanoscale is challenging in such unlikely material pairings. Significant process optimization was required to achieve the desired homogeneity of the nanocomposite. However, careful analysis of the microstructure and the mechanical properties allowed identification of the underlying mechanisms governing refinement by severe plastic deformation. Based on this, a self-reenforcing refinement process was identified as mechanism enabling efficient refinement and nanocomposite formation at elevated temperatures.
The understanding of this process allows us to tailor the nanocomposite structure precisely. This is crucial, as these structural features directly translate into the nanoporous metallic foam, thereby allowing the adjustment of pore and ligament sizes, as well as the alloying content due to mechanical alloying. Some of the results are given in Figure 2.
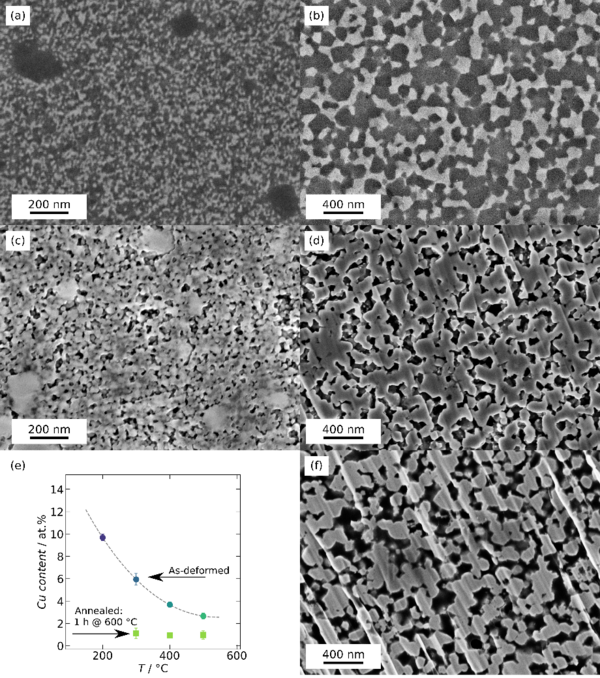
The hydrogen absorption measurements performed so far show excellent initial absorption properties of the metallic foam compared to the as-cast and crushed material, as seen in Figure 3a. Furthermore, the hydride formation is swift and reversible, allowing multiple absorption and desorption cycles of the material with a reproducible capacity (Figure 3b).

References
[1] J.J. Reilly, R.H. Wiswall, Formation and properties of iron titanium hydride, Inorg. Chem. 13 (1974) 218–222. doi.org/10.1021/ic50131a042.
[2] J. Weissmüller, R.N. Viswanath, D. Kramer, P. Zimmer, R. Würschum, H. Gleiter, Charge-induced reversible strain in a metal, Science (80-. ). 300 (2003) 312–315. doi.org/10.1126/science.1081024.
[3] K.J. Jeon, H.R. Moon, A.M. Ruminski, B. Jiang, C. Kisielowski, R. Bardhan, J.J. Urban, Air-stable magnesium nanocomposites provide rapid and high-capacity hydrogen storage without using heavy-metal catalysts, Nat. Mater. 10 (2011) 286–290. doi.org/10.1038/nmat2978.
[4] M. Sahlberg, D. Karlsson, C. Zlotea, U. Jansson, Superior hydrogen storage in high entropy alloys, Sci. Rep. 6 (2016) 1–6. doi.org/10.1038/srep36770.
Publications
Schweiger, Lukas, Daniel Kiener, et al. “From unlikely pairings to functional nanocomposites: FETI–CU as a Model System.” Materials Today Advances, vol. 20, Dec. 2023, p. 100433, https://doi.org/10.1016/j.mtadv.2023.100433.
Schweiger, Lukas, et al. “Exploring refinement characteristics in feti–cux composites: A study of localization and abrasion constraints.” Advanced Engineering Materials, 20 June 2024, https://doi.org/10.1002/adem.202400593.
Schweiger, Lukas, Felix Römer, et al. “Mechanical processing and thermal stability of the equiatomic high entropy alloy tivzrnbhf under vacuum and hydrogen pressure.” Applied Physics Letters, vol. 124, no. 24, 10 June 2024, https://doi.org/10.1063/5.0204628.