The Potential of Thermal Plasma Pyrolysis for Clean Hydrogen Gas and High Quality Solid Carbon Production from Methane
VIDEO
coming soon...
Introduction
In the contemporary landscape, the demand for natural gas (NG) as a fuel has surged owing to its high combustion efficiency and lower pollutant emissions in comparison to oil and coal [1]. However, the direct utilization of NG in the energy sector has resulted in a substantial increase in greenhouse gas emissions [2]. A statistical study reveals that the energy sector is accountable for 46% of CO2 and 82% of SO2 total emissions [1]. Given the current scenario, a projected rise in CO2 emissions from the energy sector is anticipated, escalating from 50% in 2030 to a concerning 80% in 2050 [1]. Recognizing the environmental repercussions, there is a growing interest in exploring alternatives to address energy vulnerability [1].Hydrogen emerges as a pivotal element in the pursuit of a clean and sustainable energy system. One notable characteristic of hydrogen is its diverse range of sources for production [1]. However, achieving a carbon-neutral energy source requires overcoming challenges related to the efficiency of hydrogen production technology and its economic feasibility [1]. Presently, steam reforming and coal gasification, constituting approximately 66% of the production methods, dominate hydrogen production [2]. Both methods, unfortunately, release CO2 into the atmosphere, undermining efforts to reduce emissions, with steam reforming generating about 10 kg of CO2 for every kg of hydrogen produced [2].
An alternative approach involves pyrolysis, a process that involves the decomposition of methane to produce hydrogen. The energy required for pyrolysis can be sourced through various means, such as electrical heating furnaces, solar furnaces, and the utilization of electricity to create plasmas [2]. This method offers a potential avenue to mitigate CO2 emissions associated with traditional hydrogen production methods.
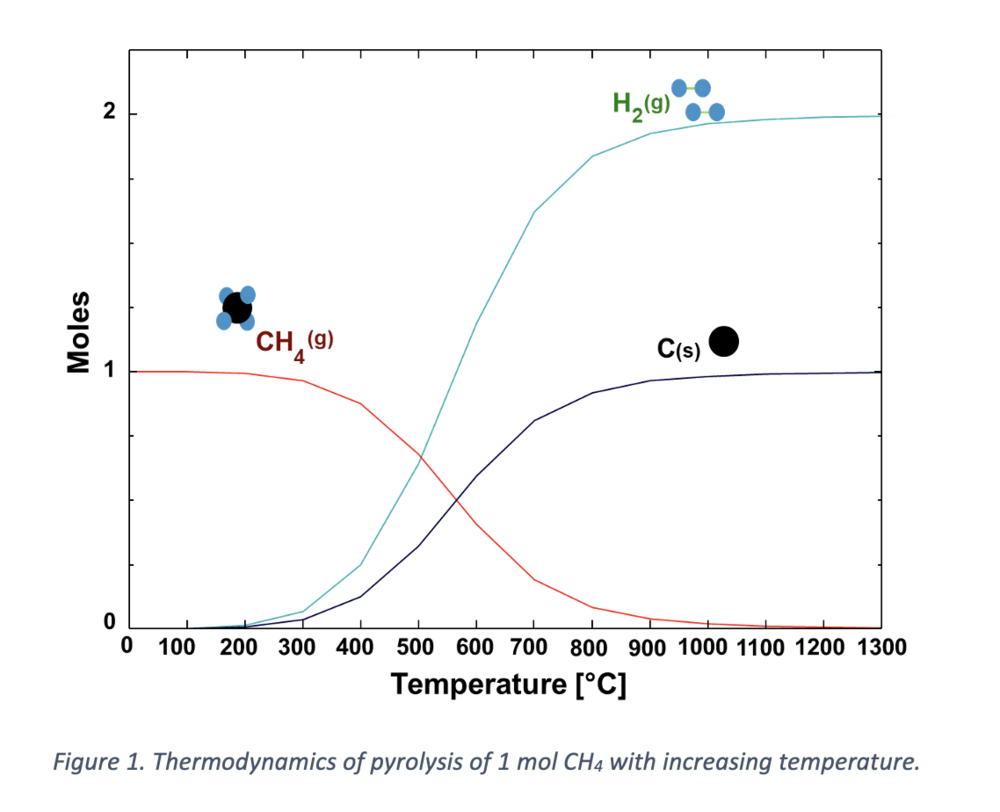
The pyrolysis process can be categorized based on its operating temperature. At temperatures below 1000 °C, methane conversion may be incomplete, necessitating the use of catalysts. These processes fall under catalytic CH4 decomposition and are typically conducted in electrical furnaces, such as fixed and fluidized bed reactors or microwave ovens. The catalysts used for this purpose are typically based on nickel, carbon, cobalt, or iron, depending on the temperature range required. However, catalysts pose a challenge as they deactivate due to carbon deposition, making regeneration difficult and potentially causing emissions. Processes operating at temperatures above 1200 °C belong to non-catalytic decomposition methods, with thermal plasma torches being an example.
Thermal plasma is a process that transforms electrical power into thermochemical energy, generating temperatures up to 9727 °C (10000 K). Its potential application includes the pyrolysis of methane (CH4), thermodynamically occurring at temperatures higher than 1200 °C. In contrast to traditional catalytic methods, thermal plasma eliminates the need for catalytic effects in the decomposition reaction. This underscores the potential of thermal plasma as a promising, effective approach for zero-carbon-emission hydrogen gas production through natural gas pyrolysis.
Apart from its capability to produce hydrogen gas with zero carbon emissions, thermal plasma technology boasts advantages like a compact design, high efficiency, and low energy requirements. Furthermore, thermal plasma facilitates the production of high-grade carbon black (CB) as a valuable byproduct alongside enriched H2 gas. CB finds applications in various industries, including mobility, plastics, and agriculture. The use of plasma in CB production is a relatively recent development, allowing the creation of new CB grades like carbon nanotubes, graphene nanosheets, and other high-quality carbon structures, with parameters that can be varied. Notably, if the electricity for the plasma is sourced from renewables and the produced carbon is entirely utilized in other sectors, the process achieves the crucial goal of a zero carbon footprint.
Theory and Objectives
A process concept needs to be meticulously developed for the viable pyrolysis of CH4, ensuring the production of enriched H2 gas and high-quality carbon. This process design should prioritize achieving maximum stability for continuous production while optimizing utilization and reaction rates. The valuable carbon byproduct holds the potential to offset production costs. Figure 2 illustrates a comprehensive study matrix for the project, highlighting the key focus areas mentioned above.
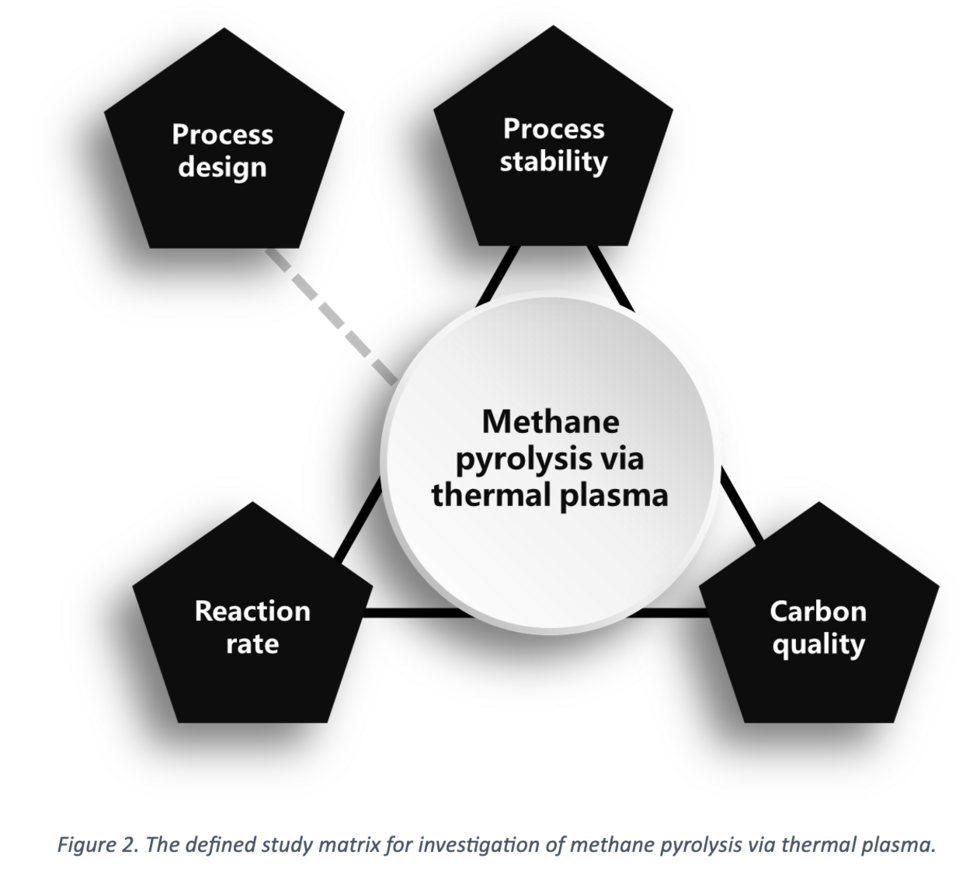
Establishing qualitative relationships between process parameters and the utilization rate or the quality of the produced carbon is a paramount objective. To achieve this, preliminary tests were conducted using a thermal plasma facility situated in the laboratory of the Chair of Ferrous Metallurgy at Montanuniversitaet Leoben. The subsequent section provides a detailed overview of this facility and its specifications.
Experimental
The Thermal Plasma Lab facility, featuring a DC transferred arc, played a pivotal role in our experiments. The reactor allows the introduction of various gas components such as Ar, CH4, and N2 through the hollow cathode positioned at the top. The electric discharge occurs between the cathode and the graphite anode pin. Notably, the flexible arc distance, spanning 1 to 6 cm, enables a power supply ranging from 3.5 to 16 kW. Figure 3 provides a visual representation of the facility and the process layout.
The pyrolysis test procedure unfolds as follows:
- Purging the entire reactor with Ar.
- Shifting the cathode to the arc ignition position, initiating a short circuit.
- Igniting the arc using Ar as the plasma gas and promptly returning the cathode to a stable arc distance position.
- Monitoring the stable arc through the camera installed on the top window of the lid.
- Introducing CH4 to the transferred arc by transitioning the gas from pure Ar to a mixture of Ar and CH4.
- Monitoring the reaction using the gas analysis device installed on the off-gas pipeline.
- Halting the CH4 flow upon completion of the intended test and transitioning to 100% Ar.
- Powering off and discontinuing the plasma gas flow.
- This systematic approach allows for precise control and observation throughout the pyrolysis test, facilitating a comprehensive understanding of the process dynamics.
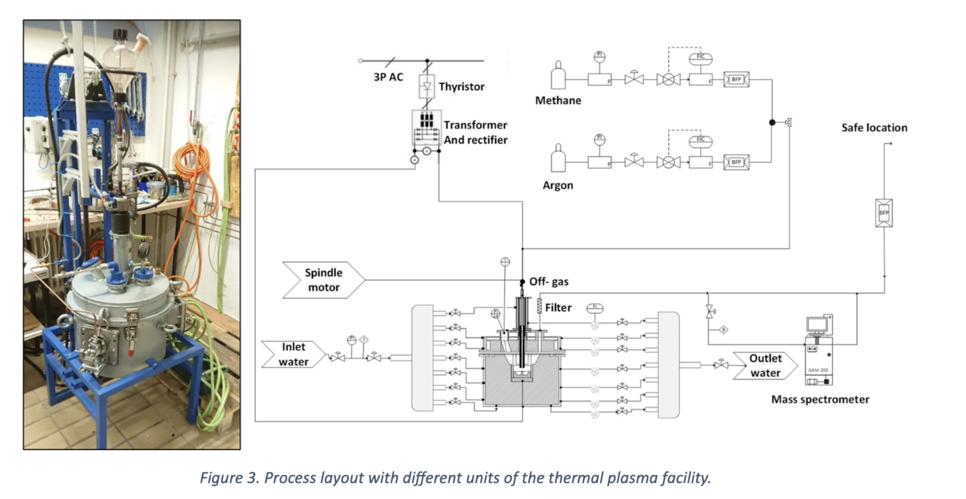
Results
Various tests were conducted to assess the viability of the process across different variables. In Figure 4, the current level, indicative of the H2 output, is depicted. Notably, an increase in current from 85 to 135 A (left) results in a notable enhancement of approximately 10% in the H2 output (right). This improvement can be attributed to the higher energy input for the pyrolysis reaction.
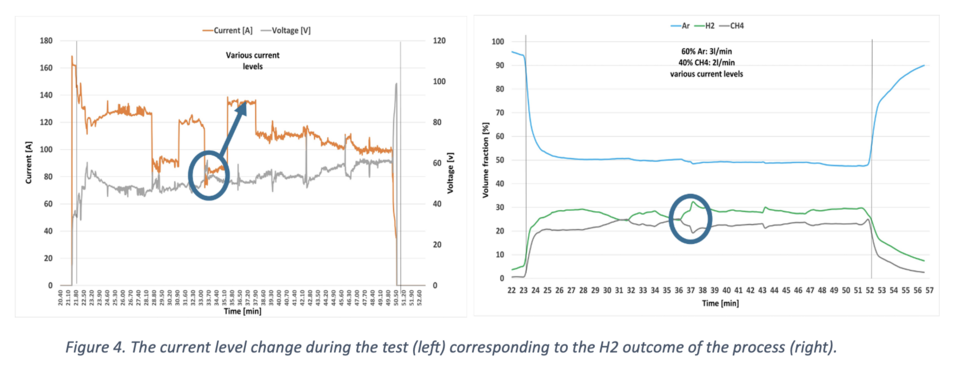
The collected carbon samples underwent thorough examination through morphological and chemical analyses, employing a scanning electron microscope (SEM). Figure 5 provides a visual insight into the reaction chamber post-test, where carbon particles are visibly attached and grown on the inner surface and the SEM images.
This multifaceted analysis not only quantifies the impact of varying current levels on H2 output but also offers a detailed understanding of the morphological and chemical characteristics of the generated carbon. Such insights contribute significantly to refining and optimizing the pyrolysis process for enhanced efficiency and product quality.
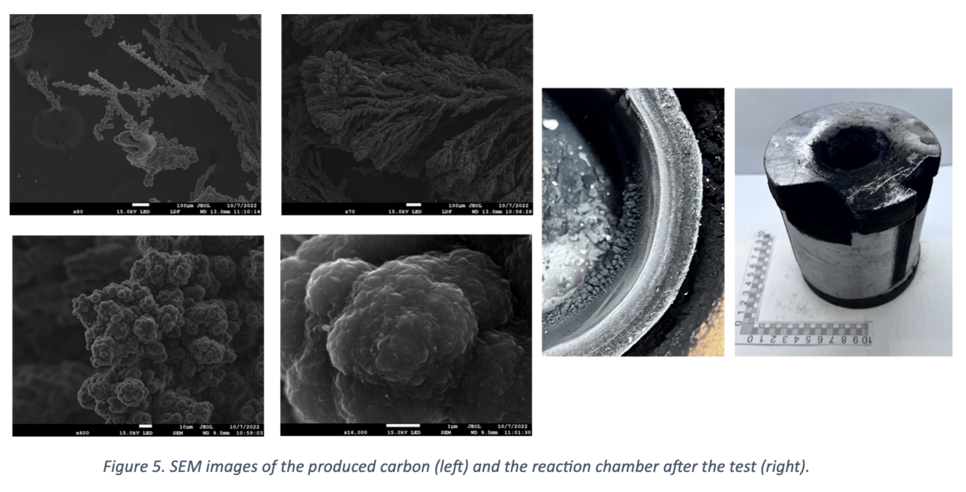
Outlook: A noble concept for H2 Production
The experimental study underscores the technical feasibility of methane plasma pyrolysis. However, a meticulous and comprehensive examination is imperative to pinpoint and monitor the influential process parameters. A refined understanding of the process is essential for its progressive development.
Building on insights from the pre-trials, several key enhancements emerge:
- Vertical Design: Facilitating a clean reaction zone.
- Water-Cooled Reactor: Preventing refractory contamination.
- External CH4 Inlet: Extending electrode life.
- Adjustable Electrodes: Facilitating the use of different electrode materials.
- Moving Electrodes: Enabling in situ shifting.
- Various Gas Components: Conducting different trials.
- High Power Input: Resulting in a higher production rate.
These strategic modifications not only address existing limitations but also open avenues for further exploration and refinement, paving the way for an optimized and efficient methane plasma pyrolysis process. A schematic representation of the conceptual design is presented here.
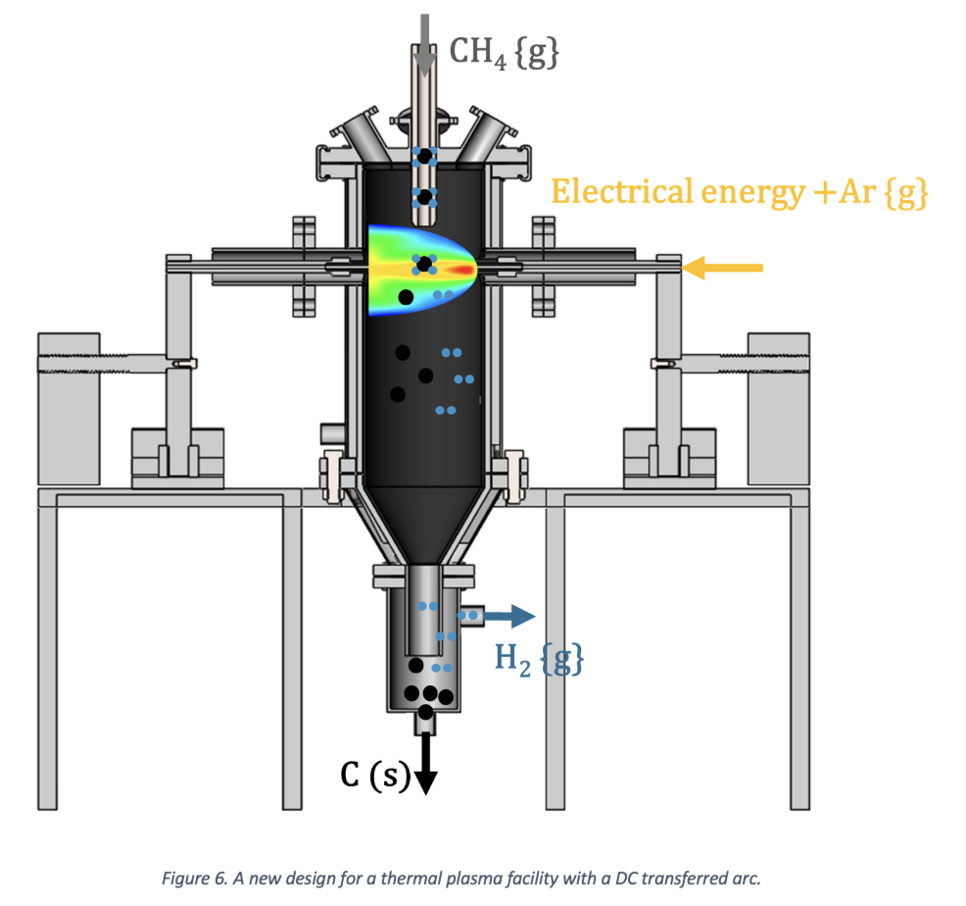
Publications / Poster
References
1] T. Da Silva Veras, T.S. Mozer, D. Da Costa Rubim Messeder dos Santos and A. Da Silva César, Hydrogen: Trends, production and charac-terisation of the main process worldwide. International Journal of Hydrogen Energy 42 (2017), 4, pp. 2018–2033. doi:10.1016/j.ijhydene.2016.08.219
[2] A.R. Da Costa Labanca, Carbon black and hydrogen production process analysis. International Journal of Hydrogen Energy 45 (2020), 47, pp. 25698–25707. doi:10.1016/j.ijhydene.2020.03.081
[3] H. Karimi, M.R. Khani, M. Gharibi, H. Mahdikia and B. Shokri, Plasma pyrolysis feasibility study of spent petrochemical catalyst wastes to hydrogen production. J Mater Cycles Waste Manag 22 (2020), 6, pp. 2059–2070. doi:10.1007/s10163-020-01089-0
[4] A. Magazova, S. Böddeker, N. Bibinov and D.W. Agar, Systematic Simulation Strategy of Plasma Methane Pyrolysis for CO2‐Free H2.